فهرست مطالب
Toggleیکی از پرسشهای متداول در کنترل صنعتی و اتوماسیون این است که «تفاوت میان سیستمهای PLC و DCS در چیست؟» برای درک تفاوت بین این دو سیستم باید نگاهی به تاریخچه آنها انداخته و اجزای درونی آنها را بررسی کنیم. تفاوت کلی میان PLC و DCS در این است که PLC برای کنترل “یک دستگاه” به کار میرود؛ اما از DCS برای کنترل “چندین دستگاه” در یک پروسه صنعتی استفاده میشود. این تنها یک توصیف کلی از تفاوت میان این دو سیستم است و در ادامه، شرح دقیقتری از آن ارائه خواهیم کرد.
یادگیری اصول اتوماسیون صنعتی و نحوه کار با PLC از مهارتهای سودمند در حوزه صنعت است. اگر به مبحث اتوماسیون صنعتی علاقمند هستید و میخواهید به صورت عملی نحوه اجرای سیستمهای اتوماسیون را یاد بگیرید، میتوانید در دورههای اتوماسیون صنعتی ماهر و اتوماسیون زیمنس ماهر ثبتنام کنید.
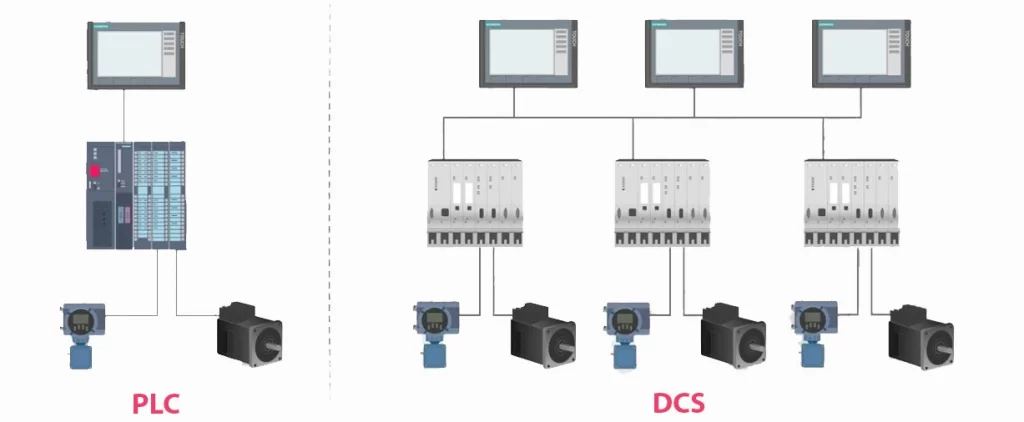
تاریخچه PLC
«کنترلکننده منطقی برنامهپذیر» (PLC) بهمنظور جایگزینی سیستمهای کنترلی قدیمیتر که بر مبنای رله و کنتاکتور بودند، ابداع شد. در حالی که «سیستمهای کنترلی توزیعیافته» (DCS) بهمنظور فراهم کردن امکانات بیشتر برای سیستمهای اتوماسیون صنعتی مبتنی بر PLC به وجود آمدند. هدف از ابداع سیستمهای DCS، جایگزینی PLCها نبود؛ بلکه هدف از طراحی این سیستمها، همافزایی با PLCها و بهبود عملکرد و کارایی تاسیسات و کارخانههای صنعتی بود.
اساساً PLCها به دلیل عدم انعطافپذیری و زمانبر بودن عیبیابی و تعمیرات در سیستمهای کنترلی قدیمی به وجود آمدند. عیبیابی سیستمهای سنتی به دلیل نوع اتصالات، سیمکشی زیاد و نقشههای پیچیده، بسیار دشوار بود. سیستمهای قدیمی برای اجرای فرامین، از تعداد زیادی رله استفاده میکردند و این بهمعنی وجود یک اتاق یا یک تابلو پر از رله، پر از ترمینال و سیمکشی بود. تعداد زیاد رلهها و کنتاکتورها در سیستمهای سنتی، یادآور ضربالمثل قدیمی “five hours to find it, five minutes to fix it” در زبان انگلیسی بود. معنای تحتاللفظی این ضربالمثل چنین میشود که: «پنج ساعت طول میکشه پیداش کنی، پنج دقیقه طول میکشه درستش کنی!!».
بنابراین، به روش متفاوتی برای پیادهسازی سیستمهای کنترلی نیاز بود که زمان توقف سیستم به دلیل خرابی را کاهش دهد، توانایی کار در محیطهای صنعتی با سطح آلایندگی، رطوبت و گرد و غبار بالا را داشته باشد و امکان توسعه ماجولار سیستم را نیز فراهم کند. در سال ۱۹۷۱، شرکت «آلن بردلی» (Allen Bradly) طراحی جدیدی بهنام Bulletin 1774 PLC را ارائه کرد که از اولین تلاشهای شرکتهای صنعتی برای طراحی PLC بود.
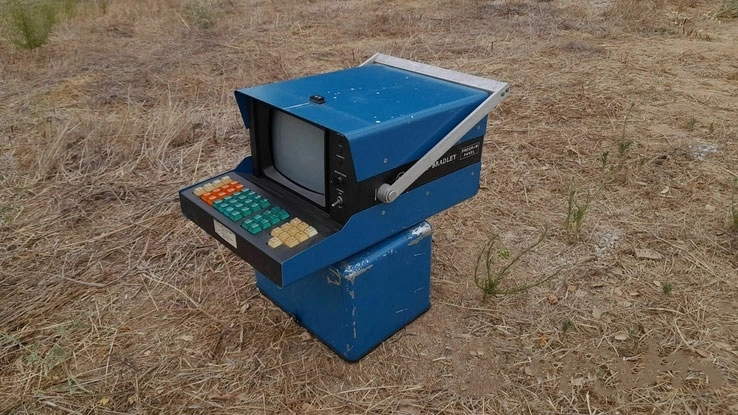
همراه با موج طراحی و نوآوری کمپانیهای دیگر در ساخت PLC، آلن بردلی هم به کار روی این ایده ادامه داد. البته از شخصی به نام «ریچارد مورلی» (Richard Morley) که برای کمپانی «مودیکون» (Modicon) کار میکرد نیز گاهی بهعنوان پدر PLC یاد میشود. او کسی بود که زبان لَدِر (Ladder-logic) را برای برنامهنویسی PLC طراحی کرد.
برای درک تفاوتها و مزایای زبان لدر نسبت به دیگر زبانها میتوانید مقاله زیر را مطالعه کنید.
تاریخچه پیدایش DCS
در اوایل دهه ۱۹۶۰ میلادی کنترل فرایندهای صنعتی هنوز در حال توسعه بود که شرکت Chemical Imperial Industries سیستمهای آنالوگ خود را با کامپیوتر جایگزین کرد. این به آن معنی بود که کامپیوترها عملاً میتوانند وظایف کنترلی را بهجای سیتمهای کنترلی آنالوگ انجام دهند. این روش به نام کنترل دیجیتال مستقیم (DDC) نامگذاری شد و کارایی مقرونبهصرفه و مؤثری را از خود نشان داد. زبان برنامهنویسی DDC در زمان خود رشد چشمگیری داشت. این سیستم به دلیل سادگی آن، در اتوماسیون ساختمانها مانند اتوماسیون سیستم گرمایشی و تهویه هم شهرت زیادی پیدا کرد. حتی سیستمهای DCS امروزی هم بر مبنای زبان DDC طراحی شدهاند.
تا سال ۱۹۸۰ پیشرفتهای صنعتی، بر جایگزینی کامپیوتر بهجای سیستمهای کنترلی آنالوگ تمرکز داشت. این کار انقلاب بزرگی در صنعتی اتوماسیون محسوب میشد؛ اما گام بعدی ایجاد یک سیستم متمرکز بود که بتوان با آن همه چیز را کنترل کرد. کمپانی «میداک» (Midac) یکی از اولین شرکتهایی بود که با طراحی یک سیستم اتوماسیون پیشرفته برای ساختمان دانشگاه ملبورن، این تکنولوژی را به کار گرفت. این سیستم مجهز به یک میکروپروسسور برای به اشتراکگذاری وظایف و یک حافظه بود.
در دهه ۹۰ میلادی، همزمان با تسلط یافتن شرکت مایکروسافت بر بازار کامپیوتر، شرکتهای سازنده DCS یاد گرفتند که نرمافزار-محور شوند؛ زیرا دریافته بودند که ادامه استفاده از برخی روشهای سختافزاری، دیگر امکانپذیر نیست. چنانکه میدانیم، امروزه نیز سیستمهای اتوماسیون به همین روش عمل میکنند.
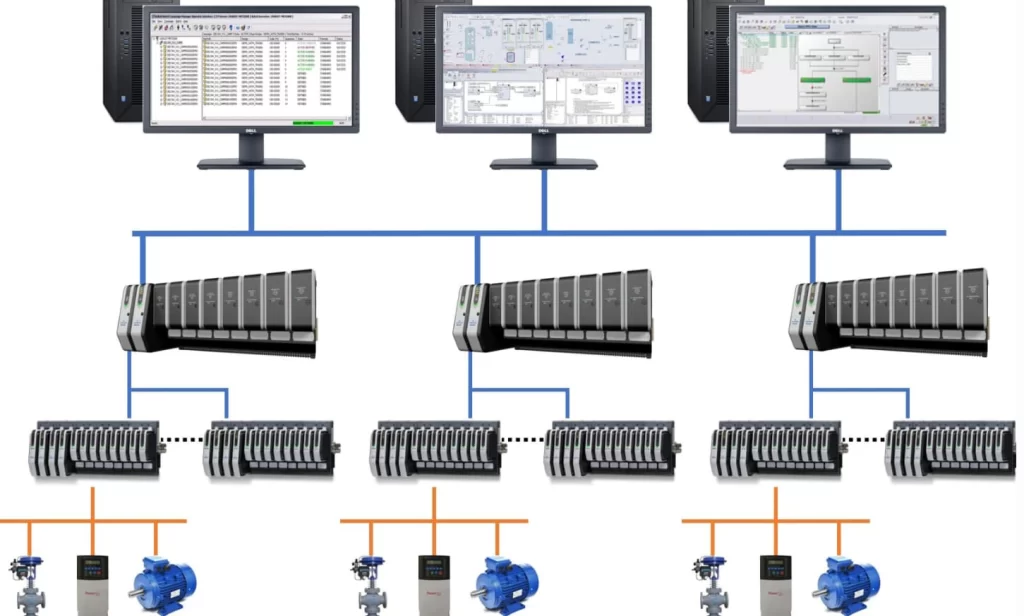
تفاوت بین PLC و DCS
پس از آشنایی با تاریخچه و هدف پیدایش سیستمهای PLC و DCS میتوان به طور دقیقتر تفاوتهای اصلی آنها را بررسی کرد. این دو سیستم کنترلی از جهات بسیاری از جمله سطح پیچیدگی سیستمهای تحت کنترل آنها، زبان برنامهنویسی و نحوه مانیتورینگ با هم متفاوت هستند.
پیچیدگی سیستم تحت کنترل
PLC سیستم عامل نسبتاً سادهای دارد. این تجهیز میتواند بهصورت سریعی برنامه را اجرا کند؛ زیرا هیچ برنامه دیگری در پسزمینه وجود ندارد که PLC بخواهد به آن هم رسیدگی کند. وظیفه PLCها کنترل یک دستگاه خاص است؛ به این معنی که تمام توجه یک PLC به کنترل عملکرد تنها یک دستگاه تمرکز دارد. بنابراین، نحوه کار PLC نسبت به سیستم DCS که چندین دستگاه را در ابعاد گسترده کنترل میکند، کاملاً متفاوت است.
زبان برنامهنویسی
PLCها بسیار منعطف هستند و میتوان آنها را برای انجام هر کار مورد نیاز تنظیم کرد؛ در حالی که سیستم DCS چنین نیست. در PLC از زبانهای برنامهنویسی سطح پایین استفاده میشود. این زبانها سادهترند و تعداد فانکشنهای کمتری دارند. از جمله این زبانها میتوان لدر، FBD و STL را نام برد. برنامههای نوشتهشده در PLC فوقالعاده کوچکتر از برنامههای نوشتهشده برای یک سیستم DCS هستند. در سیستمهای DCS از برنامهنویسی سطح بالا مانند CFC برای برنامه کنترل و مانیتورینگ استفاده میشود. مشکل برنامهنویسی سطح بالا این است که حجم بالایی از کد را به CPU اعمال میکند که باعث کاهش سرعت پاسخ به ورودیهای مهم سیستم میشود.
در مقاله زیر، میتوانید با انواع زبانهای برنامهنویسی PLC آشنا شوید.
نحوه مانیتورینگ
سیستم مانیتورینگ PLCها با سیستم مانیتورینگ DCS بسیار متفاوت است؛ زیرا در PLC هیچ رابطهای بین برنامهنویسی کنترلی و محیط مانیتورینگ وجود ندارد و طراحی و برنامهنویسی آن به صورت جداگانه انجام میشود؛ اما سیستم DCS دارای یک پکیج نرمافزاری یکپارچه، شامل تعدادی امکانات مانیتورینگ است. فانکشنهای کنترلی در محیطی قرار دارند که المان گرافیکی متناظر با آنها همزمان به صورت اتوماتیک در برنامه HMI ساخته میشوند. نحوه طراحی سیستم مانیتورینگ در DCS به گونهای است که از اتلاف زمان در هنگام برنامهنویسی جلوگیری میکند.
برند زیمنس از بزرگترین تولیدکنندگان تجهیزات اتوماسیون از جمله سیستمهای PLC و DCS به شمار میرود. در مقاله زیر با انواع PLCهای این برند آشنا شوید.
جمعبندی
PLCها مهمترین تجهیزات کنترلی در سیستمهای اتوماسیون صنعتی مدرن هستند. از این تجهیزات برای کنترل ماشینآلات صنعتی استفاده میشود. وقتی ابعاد یک پروسه صنعتی خیلی وسیع باشد، PLC قادر به کنترل همه بخشهای کنترلی آن نخواهد بود. در این مواقع، از سیستم کنترل توزیعشده (DCS) استفاده میشود. این دو سیستم کنترلی تفاوتهای عمدهای با هم دارند. در این مقاله، ابتدا تاریخچه و هدف از پیدایش سیستمهای PLC و DCS را شرح دادیم و سپس تفاوتهای مختلف میان آنها از لحاظ نحوه مانیتورینگ، زبان برنامهنویسی و سطح پیچیدگی کنترلی را بهطور مختصر بررسی کردیم.
سوالات متداول
در صنایعی که تعداد لوپهای کنترلی و تجهیزات زیاد است و ابعاد فیزیکی سیستم وسیع است از DCS استفاده میشود. مانند صنایع نفت، گاز، پتروشیمی و نیروگاههای بزرگ.
PLC سیستم متمرکز است، اما DCS به صورت توزیعشده عمل میکند و کنترل را بین واحدهای مختلف پخش میکند.
ابعاد سیستم، تعداد دستگاهها و لوپهای کنترلی، هزینههای اجرا، حساسیت پروژه از نکات مهم در انتخاب نوع سیستم کنترل است.
با سلام و خسته نباشید
آیا آموزش DSC هم جزء برنامه مجوعه ماهر هست؟
درود بر شما
در دوره های منتشر شده آکادمی ماهر تا بحال جزو سرفصل های آموزشی نبوده است